As a fellow handpan fanatic, I like these devices and infrequently marvel: how does a handpan work? What are handpans made from? And easily, learn how to make a handpan?
I’ve been lucky to have the ability to go to a couple of handpan workshops and speak to some makers to know the fundamentals! I’m not a maker, and I will not be capable of give sufficient element for different makers on the lookout for ideas. However for different handpan lovers like me, this abstract offers you an thought of how handpans are made.
First Step: Begin with a flat metal of sheet. A variety of makers purchase skinny, sq., metal sheets. Metal is made from carbon and iron. Makers normally have a choice of precisely the kind of metal they use, with the precise carbon to iron ratio.
Second Step: “Sink the shell”. This implies, make the principle dome form of the handpan. There are a pair completely different strategies that makers use. Essentially the most primary technique is to hammer it by hand, hammering it into form. A way developed by Pantheon Metal consists of “rolling the shell”. Right here, a machine rolls across the metallic sheet, forming it into the dome form. One of many latest strategies is hydroforming. That is the place water strain pushes the metal sheet via a round mildew, inflicting the metallic to balloon out right into a dome form. You may even see makers referring to the precise approach that they “sink the shell” for his or her devices.
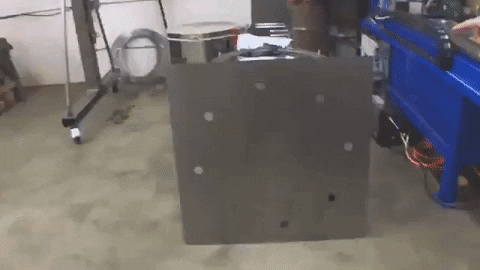
Third Step: Lower out and gas-nitride the metal sheet (now dome-shaped). Nitriding signifies that the metallic goes via a warmth and chemical response so as to add nitrogen to the metallic. The nitrating step is essential for normal metal to assist make the metal stronger and forestall it from rusting. Chrome steel devices don’t should be nitrided.
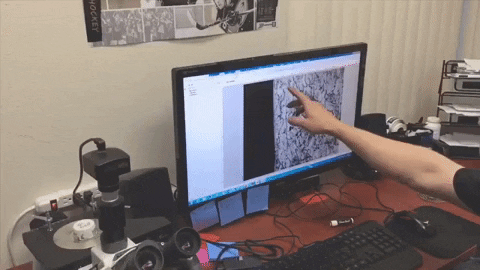
Fourth Step: Outline the dimensions and the notes that can go on the instrument and mark these on the metallic. Many manufacturers use numerous dimension molds to mark the oval space of the “tone area” on the within of the handpan shell or dome. Handpans normally have a “ding” notice and 7-9 different notes on the highest shell. These notes are normally spaced out evenly in a sure sample as deliberate by the maker. The maker can “press” or hammer the tone fields into the shell. These may be both “innie” or “outie”, additionally known as “inpex” or “apex”.
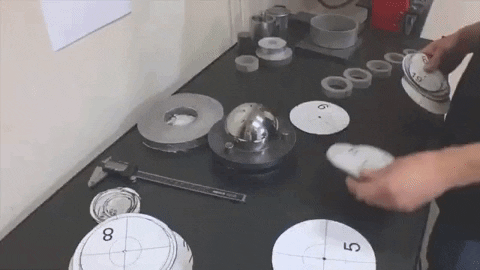
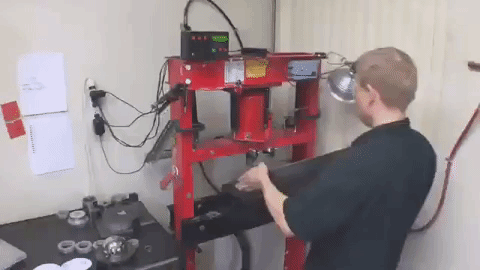
Fifth Step: Put together the handpan shell for tuning. This can look completely different from maker to maker nevertheless it usually concerned pre-stressing the tone fields to compress the metallic across the notes and heating the instrument to stabilize its newly formed structure.
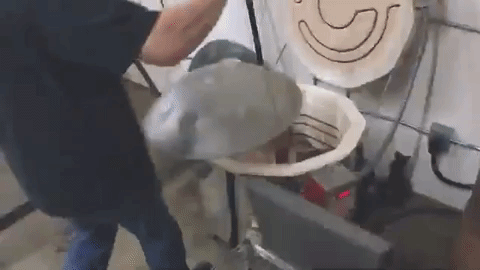
Sixth Step: Tune the handpan! This step requires an skilled tuner, and takes months and months (if not years) of apply. The principle thought of tuning is to hammer the tone area into a particular form. The best way I take into consideration the tone area is like two Pringles stacked on one another perpendicularly. The tone area has a minimum of two axis that ring a unique notice when performed. This provides the handpan an overtone-rich sound. Makers usually use software program to assist decipher the notes that ring when every axis is performed. Then they form the metallic (very subtly) to be in pitch with the proper notice for every axis. Every notice may have a elementary notice, an octave, and one other overtone—so three notes in a single!
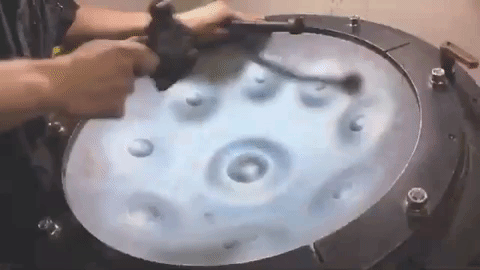
Seventh Step: Glue the highest shell to a backside shell. The underside shell is made by following steps 1-3, then chopping a gap within the center and stretching the metallic to make a port. The port needs to be the proper dimension to permit the air contained in the instrument to resonate with the opposite notes on the dimensions. That is known as the Helmholtz resonator. In different phrases, the helm can be tuned within the scale of the instrument. The underside shell might or will not be tuned with further notes (following steps 4-6 as described above). Extra warmth therapies might assist to stabilize the notes.
Eighth Step: Re-tune and fine-tune the handpan a number of instances. Let it relaxation for every week or extra between every tuning. Steel has a “reminiscence” of earlier shapes, and even after it’s formed and tuned, it desires to revert again to the way it was earlier than. Ready a pair weeks between tuning permits the instrument to “settle” barely. Then when it’s re-tuned it would maintain the brand new tuning higher every time.
Ninth Step: Clear and polish the handpan. This step isn’t required, however many manufacturers need their handpan to be stunning and able to be performed. Handpans may be cleaned utilizing a microfiber material. Some makers selected to shine the metallic by buffing it, or just utilizing somewhat lubricant (seal 1, frog lube). They will additionally take away any extra glue residue, and/or easy the tough edges or add a rubber ring. On the finish, the paradox is revealed: the handpan is a peaceable instrument born out of chaos.
I am extremely proud to companion with respected handpan makers and to supply handpans on the market proper right here on this web site. There are a number of sound fashions accessible: some are uplifting, others melancholic and but others exotic-sounding. Click on right here to view the handpans accessible now, beginning at $1,199.
Leave a Comment